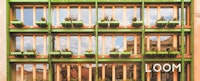
We’ve touched down in Barcelona, precisely in the 22@ District. Tasked by our client, LOOM, we undertook the complete revitalization of a historic industrial building—an erstwhile hardware store or Ferretería in Spanish—dating back to 1914, situated at Calle Pere IV 128. Covering an area of 2,500 sq. m, encompassing both ground and elevated levels, this exceptional project unfolds in two distinct phases. The initial phase involves the complete rehabilitation of the structure, followed by the second phase dedicated to establishing coworking office spaces.
The project’s extensive scope included activities ranging from excavating for the addition of the basement floor, housing services like pneumatic waste collection (ENVAC) and hot and cold water supply for installations (DISTRICLIMA) in accordance with urban regulations. This encompassed creating a new floor, elevating the existing building’s height. Additionally, casings were constructed on the rooftop to host various installations such as climate control, electrical, and photovoltaics systems. The formation of a new facade was integral to the project, featuring a primary layer composed of solid wood balconies and a secondary layer crafted in metalwork, cleverly utilizing the existing exterior pillars.
In September 2021, the second phase of the LOOM Ferretería implementation got underway. After completing various tasks related to structure and earth movement and decontamination, the focus shifted to the installation of the new facade and skylight.
Internally, we created divisions using both plasterboard and partition walls. All-new installations, including climate control, electricity, lighting, telecommunications, security, and fire prevention, were meticulously executed. Self-supporting floors, featuring ceramic, vinyl, and carpet finishes, were laid over existing slabs or newly installed raised floors. Additionally, various coverings such as tiling, painting, bricks, and acoustic panels were applied. Upon completing the structural layout, we meticulously installed custom-made workshop carpentry, along with operational and decorative furniture.
There were two key challenges in this project:
The evacuation of Class II (CII) waste involved excavating the entire footprint of the building using caissons to protect its structural integrity. The void was then carefully refilled with material sourced from a recycling plant. The excavation of the basement presented a unique challenge, requiring the suspension of primary pillars with support from micropiles and a substructure of beams.
The project has been successfully inaugurated and is a complete success. The client wisely chose a completely rejuvenated area for hosting new, modern, and innovative businesses. FLULLE has taken immense satisfaction in guiding this project through all its phases over the past 18 months, achieving an unparalleled result. We extend our sincere thanks to LOOM for once again placing their trust in us.